Facing carbon fibre bike frames
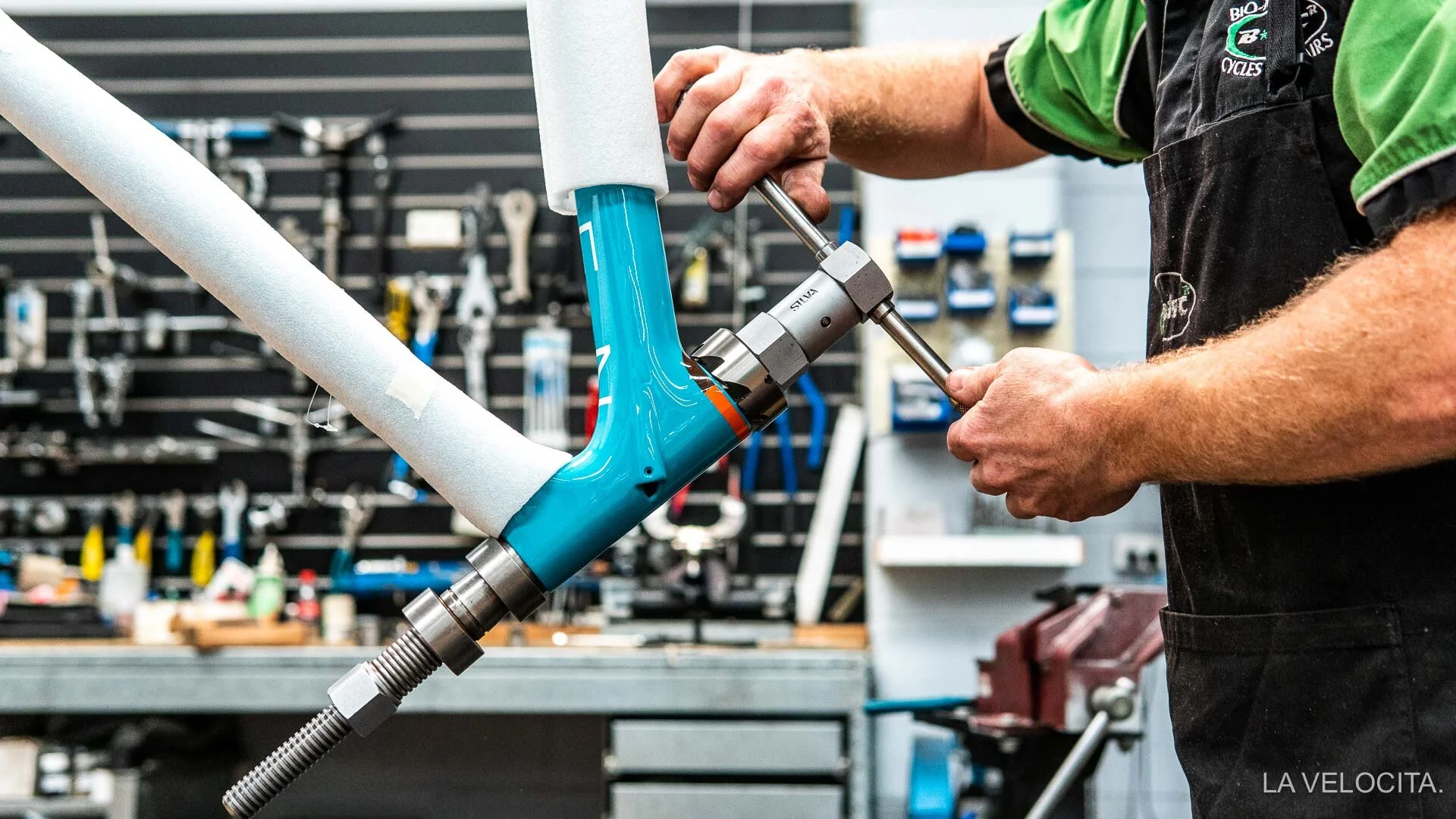
We’re back to talk about the art of facing carbon fibre bike frames; why it’s so important and why it’s so rarely done
Words and Images - James Raison
Our recent article on Facing Bike Frames was a surprise hit with readers, bringing them into the world of ultra-nerd bike builders. There was a common question from readers though: what about carbon fibre frames? A great question. The article featured an aluminium and titanium bike so naturally there was curiosity about the ubiquitous carbon fibre. In a happy coincidence, co-owner/head mechanic/chief wizard Pete from Adelaide’s Bio-Mechanics Cycles and Repairs had a carbon fibre frame that was about to go through the facing process prior to the bike’s assembly. So I went back in to take more photos, geek out, and resist the strange urge to taste the swarf.
Once again, this isn’t a paid piece or an ad, just pure bike geekery.
A QUICK REFRESHER
The first article “Facing Bike Frames; why it’s so important but few bike shops do it” was chock-full of background information on the process so we won’t cover the same information in full again. Here’re the abridged points:
Facing is the process of removing excess material from all parts of the frame, fork, and even the stem that interface with another component. In short, it makes sure every surface is flat and square before the bike gets built.
It’s necessary because most bikes leave the factory with imperfections - neither flat nor square - at those interface points. That applies to all bikes from cheap to very expensive. Exceptions are generally handmade bikes. It’s exceedingly unlikely that your factory made frame has been faced before it gets shipped and turned into your bike.
It’s important because:
On bottom bracket and headsets: It makes sure bearings are aligned properly, lengthening their life, the life of the components they touch, and reducing creaking.
On disc brake mounts: Facing makes sure the surface is perfectly flat, which is critically important for proper alignment of disc brakes. Without a flat surface it’s extremely difficult to properly align the brakes, which causes brake shrieking and uneven wear.
On stems: Perfectly flat surfaces (top and bottom) make sure there’s even pressure when the top cap pulls downwards on the upper bearing cover and spacer.
Few bike shops do it because:
The tools are expensive: Pete’s initial investment on good-quality tools in 2004 was between $15,000 and $20,000. There are hundreds of dollars more to spend ongoing with annual sharpening and maintenance on the tools.
It’s time-consuming: The process takes approximately 2 hours if all goes well. Occasionally some individual parts can be very difficult to face and take an hour alone.
New bikes can mask imperfect interfaces: Shiny new bikes with shiny new parts, freshly built, should be quiet and so buyers are mostly happy with them. With time comes the adverse effects of not facing bikes: noise and component wear.
Manufacturing business model: Imperfections in the manufacturing process are side-effects of scaling production and squeezing value into the end product. Proper facing and finishing of frames would add significant cost and time to the final build.
OPEN WIDE
Today’s frame was an Open Wide and again we’ll lead with the disclaimer that these are frames that were being built anyway, not chosen because they’re worse than others. The Open, in fact, turned out to be quite good:
“It’s actually a pity that the only frame I needed to prepare today was the Open! I would have run the cutters over it anyway but they’re generally well-finished. It was handy for the demonstration that a couple of areas — such as the brake mounts — need a little bit more work but overall they’re very accurate. Other brands vary quite a bit.”
FACING CARBON FIBRE BIKES
The first phase of preparation involves a very cheap tool: a Sharpie. Pete covers all of the surfaces he’s going to prepare with cutting tools with a layer of black marker. It’s a simple way to make an important validation.
Facing begins with a healthy coating of black marker.
“I use a black marker because that’s what I’ve always used. It’s just a way of qualifying the evenness of the surface and the accuracy of the cut. As we do a light cut, we can see the variances and the high and low points. Then I’ll start with the diamond grinder or sandpaper before going back to the cutters to see how I’m progressing. This process is repeated until the final very light cut shows that all of the ink has been removed from the surface, proving this part of the bike is completed.”
Above you can see where the cutters have shaved off the texta marks.
Facing carbon fibre is conceptually similar to any other frame material but its process is far more challenging because of the material. It’s visibly much slower and gentler than with metal frames though. The head tube and bottom bracket facing use same hefty Silva cutters slotted through the frame and secured in place with a tensioning spring and threaded bolt to hold everything in place. The difference is in Pete’s hands. Cranks of the cutter’s handles are lighter and slower. There’s clear concentration on his face as he monitors feedback from the frame, repeatedly undoing the cutter and checking the facing surface. The aluminium and titanium frames I watched him face the previous time are done with more decisive turns, and a healthy application of cutting oil.
Carbon fibre shavings slowly build up on the cutter
The first challenge in facing carbon fibre is that dedicated carbon-fibre cutting tools don’t exist;
“Bicycle-cutting tools are very specific. There are plenty of carbon-fibre cutting tools and facing tools for other industries but not for the bicycle industry. It’s a small market so carbon-specific cutters are just not produced on a commercial level. As we’ve seen from some of the comments on the last article [including from bike shop owners and mechanics] not everybody is interested in the facing process or believes it needs to be done. So it’s really catering to people like myself who want to do the best job we can. I’ve been talking with a couple of toolmakers to see if we can do some proprietary cutters but they’d be horrendously expensive. Because of that we use conventional cutters with diamond grinders and even sandpaper — carbon is very accommodating to abrasive materials. We still need the cutters for the final finishing so we can make sure the surfaces are flat and square.”
Carbon shavings and the intimidating cutting surfaces
Why is carbon an inherently hard material to cut?
“Carbon is very abrasive and very hard on the cutting tools so sometimes we need to take a different approach depending on how out-of-square the frame is. That said, carbon is a material used throughout the world for many applications so there’s absolutely no reason why you can’t face a carbon frame using the same process you would for a metal frame.”
Facing the headset and the bottom bracket were simple: the cutters shaved out a small amount of excess material and the Sharpie marks were eradicated, indicating a level surface. Things got more interesting on the disc brake mounts.
The first cuts on the disc brake mounts are made by these tiny Park Tools cutters
THE DIAMOND CUTTER
The Park Tools cutters and drill were brought out for the disc brake mounts. The initial cuts showed unevenness. The picture lower down shows the left mount with clear high and low points indicated by where the sharpie marks have disappeared and where they still remain. The discrepancy means getting out the diamond cutter.
“It’s [the diamond cutter] a small barrel of high-speed steel which has diamonds impregnated into its surface. It’s very hard, very abrasive, works beautifully with carbon (as you saw) and makes the job so much easier. We can only use it in certain areas — non-integrated head tubes, BB shells and disc brake mounts, for example. You’ve got to have a very delicate touch because if you slip you can make a massive mistake and potentially destroy a frame. It’s not suitable for all areas (such as integrated headset bearing seats) but it makes life a lot easier. ”
Pete works the cutter over the mount point to flatten it off tenths-of-a-millimeter at a time before passing the cutters over the second mount and using the diamond cutter again, swapping back and forth between the tools until he’s satisfied. The process is repeated for the brake mounts on the fork. The process takes approximately 2 hours, and the Open’s surfaces are flat, parallel and ready to build.
The remaining texta marks on the left brake mount show Pete where the diamond cutter is needed. The right is untouched and still covered in black.
THE FAQs
Following the facing I ran through some of the questions asked by readers of the first article.
Does facing void warranty?
“Most manufacturers don’t have a problem with it. They understand the need for it. Component manufacturers pretty much state that frames should be prepped before their parts are fitted. There’s an expectation that the frame needs to be squared and finished properly before you do the assembly. There are acceptable tolerances, of course — it’s not like we’re working in the medical or aerospace industry so there’s room for variance — but they want you to get as close as possible.”
Pete sent me through some install manuals for components to back up his statement that component brands want, and recommend, facing to be done. Below are some examples.
White Industries bottom bracket: “It may be necessary to chase the bottom bracket threads and have each side of the bottom bracket faced in order to ensure that the bottom bracket can be installed and adjusted properly. Your local bike shop has the tools to do this if you don’t.”
Chris King headset: “Ream and face the head tube to ensure that the ends are square and parallel to each other, and the head tube bore (inner diameter) is correct (see table below) to ensure proper press fit. Minimum ream depth is 25.4mm into the head tube.”
Campagnolo bottom bracket: “Face the bottom bracket shell respecting the measures X, using a suitable tool.”
SRAM bottom bracket: “For best results, have your frame machined and faced by a professional bike mechanic.”
Some people asked about threaded bottom brackets: are they any different? Or do they need less preparation?
“It’s exactly the same. Frames need to be square. It doesn’t matter whether it’s threaded or pressfit; you have to start with something square if you’re looking to give the best result to your customer. It’s the truth of the components as well. If the ends of the bottom bracket shell are not perfectly flat, you can feel it when you tighten up the bottom bracket cups because they’ll twist and conform to the shape of the frame. As soon as you face the shell and you’ve confirmed the cups are square you can feel them lock down against each other and there’s no movement and there aren’t going to be any clicking issues.”
So far we haven’t seen a fork prepared. Can you tell me about that process and how it relates to the stem and headset facing you do?
“We start with the stem and make sure it has two parallel faces. We can then work with spacers (if there are any) and make sure that the head tube is perfect so the bearings are sitting parallel to each other. Where we can, we’ll qualify, and face if necessary, the fork crown so all surfaces are parallel. As we pull down from the top cap we’ll have completely even pressure. The bearings sit nicely in the frame; you’ve got even steering so when you spin the fork there are no variances in the feel, no tight or loose spots. More importantly the bearings hold their adjustment. We’ll see bikes come in with a customer reporting the headset always comes loose after a few rides, and we’ll start looking at whether the bearings seats are square because it’s never going to hold its adjustment if things are out.”
What are your thoughts on the response to the last article, both positive and negative?
“It’s good that there’s interest. Some of us are truly dedicated to getting as close to perfect as we can. People who don’t see the need for it who work in the bicycle industry… that’s fine. If they don’t see it as important and they’re happy, and their customers are happy, then good luck to them. It’s not that one way is definitively right and that one is definitively wrong. It’s the way that I choose to do it because it makes me feel good that I’ve produced the best possible product I can. It’s just my personality type.
For us when we’re selling bikes, whether it’s a $1,500 bike or a $15,000 bike, they all get the same time spent on the frame. Those cheaper bikes, in real terms, we sell at cost. I’m happy to do that because I’m happy with the product. If I was looking at it purely from a numbers perspective, of course I wouldn’t face the frame and fork because then you cut the build time down by hours.”
THE NECESSITY OF FACING
We read multiple comments about facing being “unnecessary” from people who identified as current or former shop owners and mechanics, and many who were passionate bike owners. The truth is that facing is not strictly necessary for a bike to function. No arguments there. That said, facing makes a bike better through its lifetime. Components will last longer, require less maintenance, and make less noises. To disagree is to fundamentally reject the idea that flat and parallel surfaces are a better start to building a bike than ones that aren’t flat and parallel.
On a personal note, this has been rewarding content to make. I’ve spent many thousands of dollars on frames with sloppy finishing. Their creaks, squeaks and squeals have driven me bonkers. We as bike buyers don’t have to like that our beloved steeds are riddled with imperfections, but they are. To assume perfection on the basis they’re new and/or expensive is naive and, in the vast majority of cases, incorrect. Don’t be mad at us, that’s how the sausage gets made.
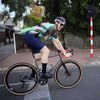